Chicago-based International Harvester grew out of Cyrus Hall McCormick’s 1831 invention of the mechanical reaper. In 1904, the farm machinery business began manufacturing trucks, and, in 1937, Harvester consolidated motor production by building a foundry and an engine plant on a 75-acre site on the southeast side of Indianapolis. Employing 1,100 people, the plant produced its first engine in 1938.
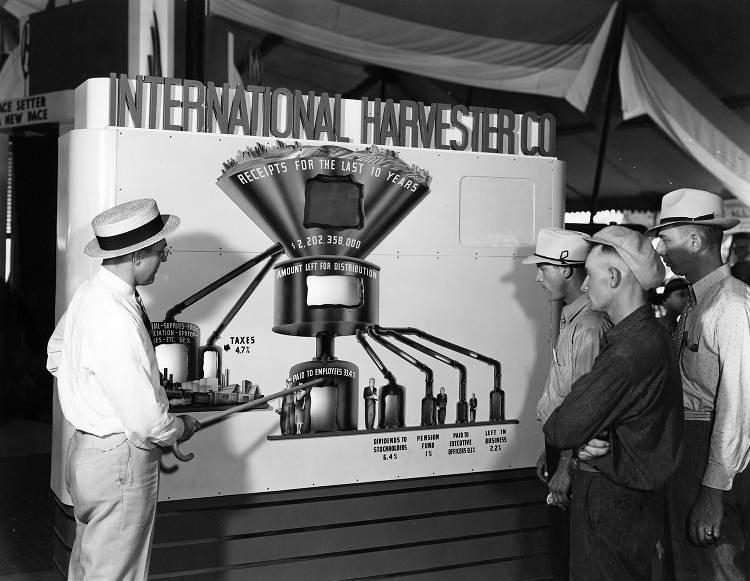
During World War II, the plant operated nonstop, manufacturing engines for military vehicles, mounts for Navy anti-aircraft guns, and track shoes for Army personnel carriers. By 1946, plant employment had increased to 4,450 people.
The Indianapolis plant continued manufacturing engines during the 1950s and 1960s, but, by the late 1970s, Harvester began losing its competitive edge. Financial troubles forced it to stop the production of vehicles using engines made at the Indianapolis plant. In 1981, engine production in Indianapolis dropped to 28,000 as compared to over 200,000 annually in the early 1970s. Employment also dropped, from over 3,400 to less than 1,000.
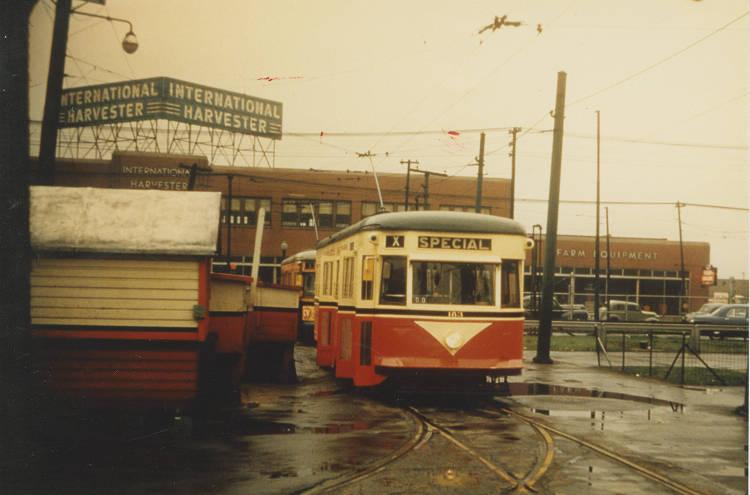
A 172-day strike in late 1979 and early 1980 caused company officials to consider abandoning the plant and moving production to Mexico in favor of lower labor costs. To save the plant, the city and state contributed $2.1 million in loans and job training, and the union agreed to wage and benefit concessions. Rejuvenated, the plant began production of a new engine, used by the
in vans and pickup trucks, and became a money-maker for Harvester.In 1986, International Harvester changed its name to Navistar International, reflecting the sale of its farm equipment business. In 1991, the plant’s foundry, known as the Indianapolis Castings Corporation, became a wholly-owned subsidiary of Navistar. By the early 1990s, Navistar’s Indianapolis engine plant employed over 1,900 people (700 at Indianapolis Castings) and had annual sales of more than $350 million.
Navistar ceased operations of the engine plant in 2009, after Ford shifted the assembly of diesel engines from Navistar to its own plant in Mexico, but kept its plant in Indianapolis open. The company continued to operate the facility’s foundry making engine blocks and heads.
In 2010, United Auto Workers Local 226 members who worked at Navistar agreed to a 40-percent pay cut in an attempt to save the facility. The company agreed to spend $19 million to upgrade the plant with new casting equipment over three years and to increase employment numbers in return for a savings of nearly $1 million in property taxes over seven years. In 2015, Navistar officials, however, made the decision to close the foundry stating that the company could save about $13 million buying “those castings from its suppliers” rather than making them at their own plant in Indianapolis. The foundry was shuttered at the end of June 2015, leaving 160 workers without jobs.
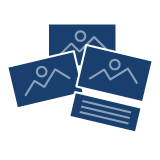
Help improve this entry
Contribute information, offer corrections, suggest images.
You can also recommend new entries related to this topic.