The events of
led Walter and John Brant to launch the Indiana Oxygen Company (IOC) in 1915. When the war in Europe threatened automobile sales, they abandoned the Brant Brothers Automobile Agency, a dealership for two early Detroit-based car manufacturers that they had founded in downtown Indianapolis in 1910, and established Indiana Oxygen as the first industrial gas production plant in Indiana. At the company, the Brants pioneered a new electrolytic separation technology introduced into the U.S. in 1907. In this process, liquid elements are vaporized and converted to gas before packaging in cylinders and shipping to the customer. The convenience, safety, and mobility of compressed gas cylinders in the electrolysis procedure succeeded the prevailing method of water molecule separation through forging, or “blacksmithing.”With Indiana Oxygen, the Brants continued a relationship that they had established with the
(IMS) when they sponsored two race cars for the inaugural running of the . In the early 1920s, Indiana Oxygen introduced compressed air, an alternative to hand-pumping racing tires, for the race. IOC subsequently began the use of nitrogen in racing tires in 1925. Nitrogen maintains air pressure longer, which results in better fuel economy and longer tire life. IOC later engineered pressurized refueling with nitrogen, a practice abandoned in 1964 because of safety concerns.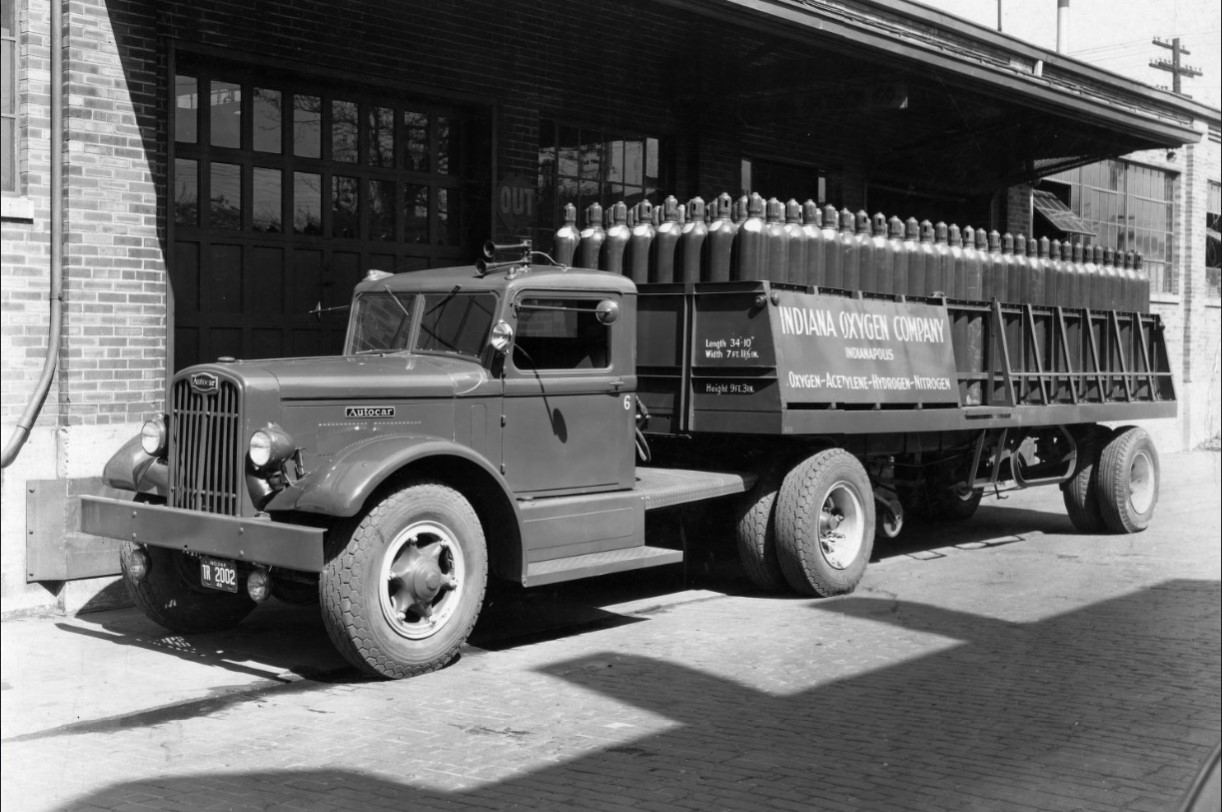
The Brant brothers expanded to Kenosha, Wisconsin, in the early 1920s with their second electrolytic oxygen-hydrogen plant, Wisconsin Oxygen-Hydrogen Company. The brothers sold this business and used the proceeds to build an acetylene-generating plant in
, Indiana, in 1925. That facility continues to operate. Moving to a larger facility in 1930, IOC adopted a new technology for atmospheric air separation that allowed the company to produce an array of atmospheric gases.In 1937, Walter Brant’s son Robert “Bob” Brant joined Indiana Oxygen. Bob Brant learned the family business from the ground up, driving trucks for the company before moving to sales then director of operations and finally president of IOC. He was chairman of the board at the time of his death in 2006.
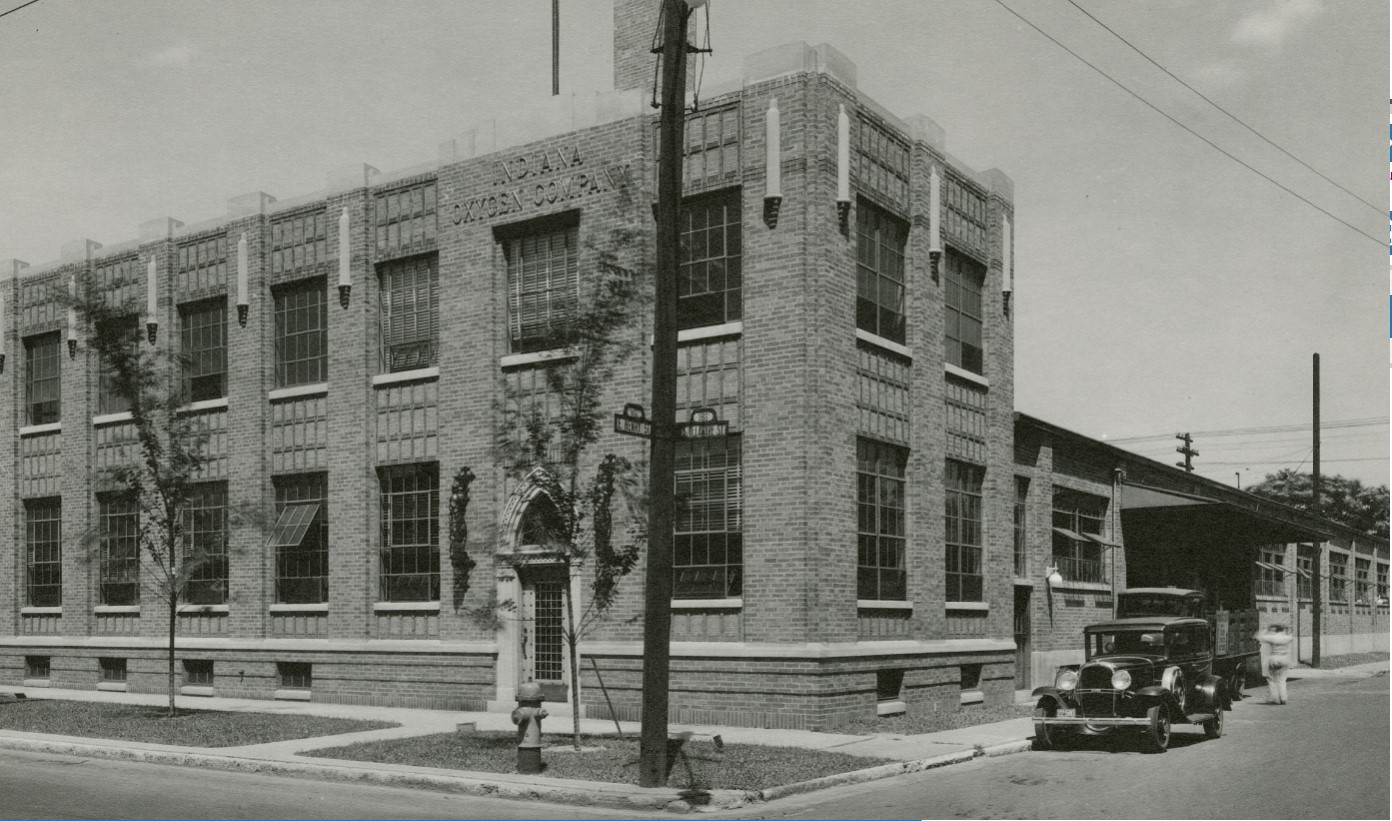
The facility Indiana Oxygen occupied in 1930 was replaced with a pumping systems facility that produced specialty gases and high purity blend gases in 1960. With myriad specialty gases, IOC again was a pioneer of these innovations in the 1960s, as it had been back in the 1920s with nitrogen. The increased demand for the new gases, which included liquid bulk oxygen, nitrogen, argon, and carbon dioxide, necessitated relocation to a new palletized fill plant on the northwest side of Indianapolis in 1991. The 1930 Indiana Oxygen building attained National Historic Register status in 1987, and it was moved from 435 S. Delaware Street to 351 East Street in 1995.
After purchasing a welding supplier in Lawrenceburg, Indiana, in 1995, IOC opened a 10,000-square-foot retail outlet near Cincinnati, Ohio, in the early 2010s, solidifying its footprint in the region. The Cincinnati location is an exception to the group of outlying IOC branches in that it produces its own products instead of transporting them from Indianapolis. Outlying branches are mainly stores where customers purchase gases and welding supplies.
Indiana Oxygen added another building to its northwest Indianapolis site in 2014 to accommodate its new e-commerce division, serving all 50 states and a dozen countries. The 31,000-square-foot building serves as a production facility and retail store.
Company-wide recycling and LED lighting throughout its facilities are two ways the company demonstrates its commitment to protecting the environment. These efforts have earned IOC Platinum-level, Green Business Bureau Certified status.
In the 21st century, Indiana Oxygen mostly provides oxygen, nitrogen, helium, and argon to its clients. The company, however, maintains its connection to the Indianapolis Motor Speedway by maintaining a garage in “Gasoline Alley” for onboard air jacks and pneumatic tools to remove lug nuts for faster pit stops. While welding continues to hold its own in the industry, gases in high tech applications present one way specialty gases drive company growth. Nitrogen is used in thermometers and to fill light bulbs. The liquid form is used as a coolant in cadaver preservation and in cryopreservation of reproductive cells and biological samples.
, for example, uses nitrogen from IOC to purify air during pharmaceutical production.Indiana Oxygen remains family owned, a fourth generation of Brants leads the company. As the oldest gas and welding supply distributor in the country, the company continues to be the largest independent gas and welding distributor in Indiana.
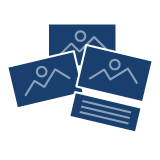
Help improve this entry
Contribute information, offer corrections, suggest images.
You can also recommend new entries related to this topic.